Exploring the Benefits of Silicone Rubber Sheets for Vacuum Press Applications
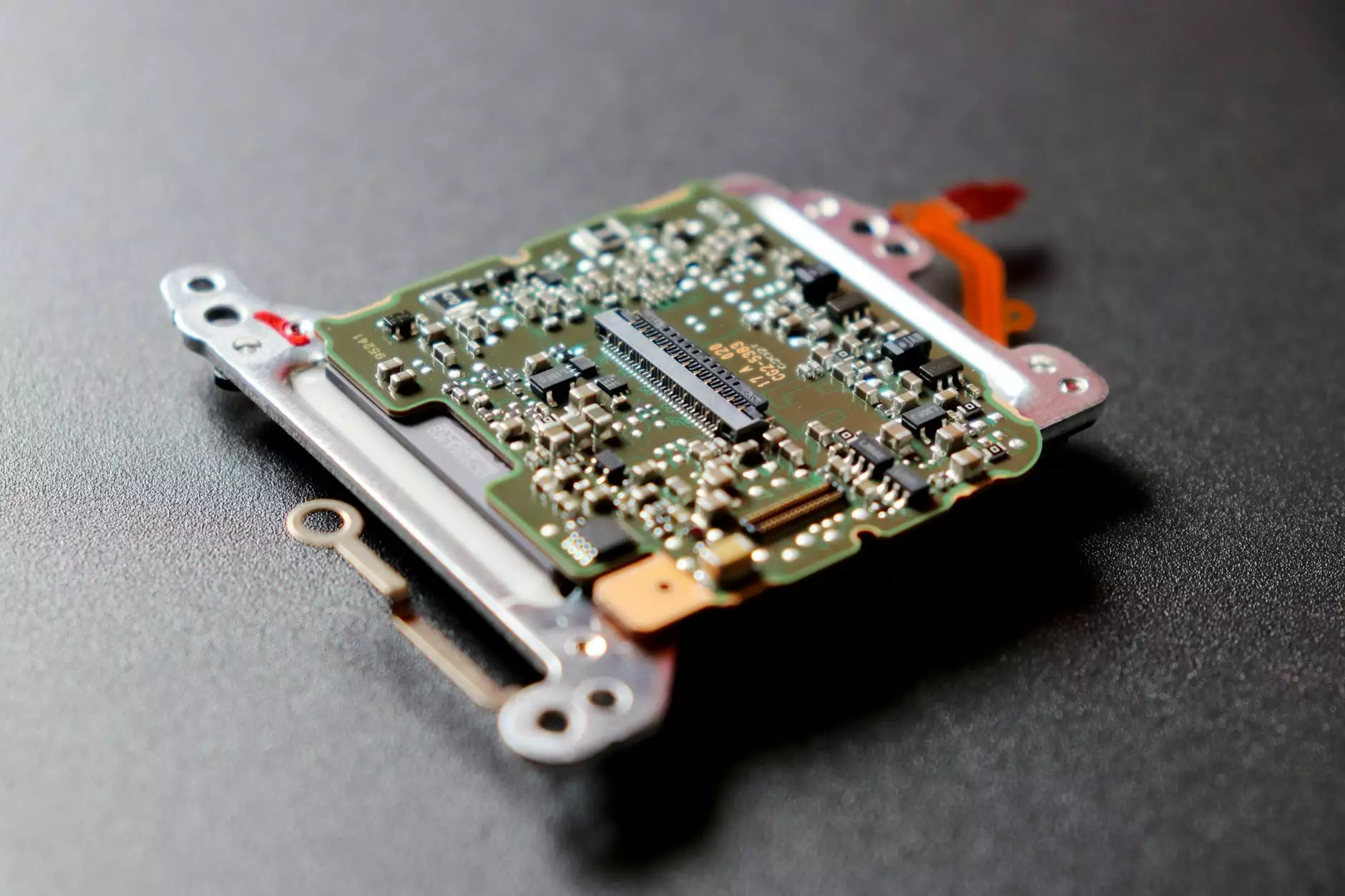
In the world of modern manufacturing, the demand for high-quality materials that can withstand a variety of uses is at an all-time high. Among these, silicone rubber sheets for vacuum press applications stand out as a versatile and reliable choice. This article delves deep into the various benefits, uses, and characteristics of silicone rubber sheets specifically designed for vacuum pressing, in relation to sectors such as Health & Medical, Beauty & Spas, and Medical Spas. Our goal is to provide comprehensive insights that can aid in your decision-making process and help you understand why these materials are essential in many industries.
The Unique Properties of Silicone Rubber Sheets
To appreciate the role of silicone rubber sheets in vacuum press applications, it is crucial to understand their unique properties:
- Heat Resistance: Silicone can withstand extreme temperatures, typically ranging from -60°C to 200°C. This makes it suitable for various applications where other materials may fail.
- Non-stick Surface: The non-stick properties of silicone help in preventing materials from adhering to surfaces, thereby facilitating easier removal after the vacuum pressing process.
- Flexibility and Durability: Silicone rubber sheets are highly flexible yet exceptionally durable, which allows them to maintain their shape and integrity over time, even under stress.
- Chemical Resistance: These sheets resist a wide variety of chemicals, making them suitable for applications requiring exposure to solvents and oils, often found in health and beauty products.
- Biocompatibility: For health and medical applications, silicone rubber is biocompatible, ensuring safety for products that come into contact with skin or bodily fluids.
Applications of Silicone Rubber Sheets in Various Industries
1. Health & Medical
The Health & Medical industry relies heavily on materials that offer unmatched safety and performance. Silicone rubber sheets play a vital role in the following applications:
- Medical Device Manufacturing: Used in the production of components for devices that require high levels of hygiene and safety.
- Prosthetics: The flexibility and comfort of silicone make it ideal for prosthetic devices, ensuring they are not only functional but also comfortable for users.
- Protective Equipment: Many items, such as face masks and gloves, incorporate silicone due to its non-toxic properties.
2. Beauty & Spas
In the Beauty & Spas sector, silicone rubber sheets are increasingly popular due to their unique characteristics:
- Facial Masks: Many skincare brands use silicone for the formulation of facial masks as they retain moisture and heat, enhancing the effectiveness of treatments.
- Tools and Accessories: Beauty tools such as flexible molds and brushes are often made with silicone, providing durability and ease of cleaning.
- Pools and Spas: Silicone rubber sheets are used in the construction of spas and pools, thanks to their resistance to water and chemicals.
3. Medical Spas
The growing trend of Medical Spas combines aesthetics and healthcare, thus requiring high-quality materials such as silicone rubber sheets:
- Therapeutic Devices: Devices used for therapeutic procedures often utilize silicone for its heat resistance and comfort.
- Cosmetic Procedures: In various procedures, silicone is used in molds to create in-situ items that align perfectly with the body.
Benefits of Using Silicone Rubber Sheets for Vacuum Press Applications
When it comes to employing silicone rubber sheets for vacuum press applications, the benefits are numerous:
1. Improved Efficiency
Using silicone rubber sheets in vacuum presses results in improved efficiency. Their ability to create a reliable seal ensures uniform pressure distribution, leading to better quality outcomes in the final products.
2. High-Quality Finish
The non-stick surface characteristic of silicone allows for a high-quality finish on pressed parts. This minimizes imperfections and surface defects, which is particularly important in industries where aesthetics matter significantly.
3. Reduced Waste
By providing a consistent and reliable vacuum seal, silicone rubber sheets reduce material waste during the pressing process. This is paramount in both manufacturing and the environment, leading to more sustainable practices.
4. Cost-Effectiveness
While the initial investment in silicone rubber sheets might seem higher than traditional materials, their longevity and reduced replacement frequency make them a cost-effective solution over time.
Choosing the Right Silicone Rubber Sheets for Vacuum Pressing
When selecting silicone rubber sheets for vacuum press applications, consider the following factors:
- Thickness: Depending on the intended application and the required pressure, select the appropriate thickness to ensure optimal performance.
- Temperature Range: Ensure the silicone material can withstand the temperatures required in your specific vacuum pressing application.
- Durometer: The hardness of silicone sheets should match the desired flexibility and durability needs of the project.
- Certifications: For health-related applications, opt for silicone that is certified as biocompatible and safe for use in medical scenarios.
Conclusion
In conclusion, silicone rubber sheets for vacuum press applications are a game changer in industries such as Health & Medical, Beauty & Spas, and Medical Spas. Their unique properties, extensive applications, and impressive benefits make them an essential material for modern manufacturing processes. With the right choice and application, businesses can experience increased efficiency, reduced waste, and enhanced product quality.
For more information and to explore a wide range of high-quality silicone products, visit silicone-membranes.eu today!
silicone rubber sheet for vacuum press