Understanding Titanium Screw Manufacturers
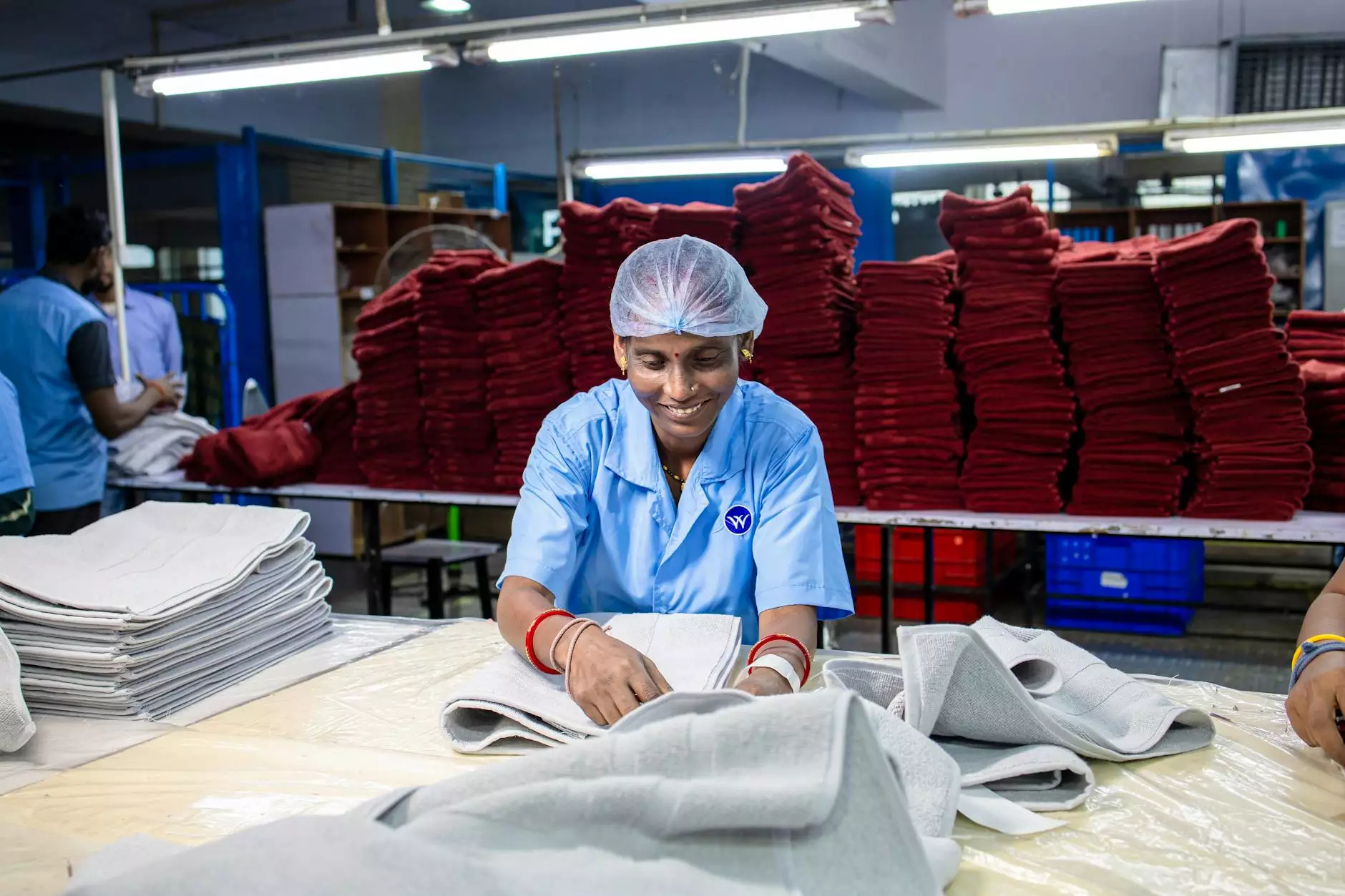
In the ever-evolving landscape of manufacturing, the role of titanium screw manufacturers stands out as pivotal. These manufacturers specialize in creating screws made from titanium, a material celebrated for its strength, lightweight properties, and resistance to corrosion. In this comprehensive guide, we will delve deep into the world of titanium screws, examining their advantages, applications, and the intricate manufacturing processes that define their production.
The Advantages of Titanium Screws
Titanium screws offer a plethora of benefits over traditional metal screws, making them increasingly popular across various industries. Here are some of the key advantages that highlight why they are a top choice:
- Lightweight: Titanium has a low density, making it significantly lighter than steel or aluminum.
- Corrosion Resistance: Titanium is inherently resistant to rust and corrosion, even in harsh environments.
- Strength: Titanium boasts an impressive strength-to-weight ratio, ensuring durability without the bulk.
- Biocompatibility: Non-reactive with the human body, making titanium screws ideal for medical applications.
- Thermal Stability: Maintains integrity and performance at a wide range of temperatures.
Applications of Titanium Screws
The versatility of titanium screws allows them to be utilized in various industries. Here are some notable applications:
Aerospace Industry
In the aerospace sector, weight reduction is paramount. Titanium screws are extensively used to secure components in aircraft, ensuring safety without compromising on performance.
Medical Sector
Due to their biocompatibility, titanium screws are often found in implants and surgical instruments, providing safe and reliable solutions for medical professionals.
Marine Applications
The resistance to corrosion makes titanium screws suitable for marine environments, where other metals would succumb to rust.
Automotive Industry
High-performance vehicles benefit from the use of titanium screws, which contribute to reduced weight and enhanced performance.
The Manufacturing Process of Titanium Screws
Understanding how titanium screws are manufactured helps in appreciating their quality and performance. The production process involves several intricate stages:
Material Selection
The first step in production is selecting the right grade of titanium. Common grades include Grade 2 (commercially pure) and Grade 5 (Ti-6Al-4V). Each grade has unique properties that suit different applications.
Forging
Titanium ingots are subjected to high temperatures and pressures in a controlled environment during the forging process, shaping them into initial screw forms.
Machining
The forged titanium pieces are then precisely machined to create the screw threads and head. CNC (Computer Numerical Control) machines are often employed for accurate dimensions.
Surface Treatment
To enhance their properties further, titanium screws undergo surface treatments like anodizing, which improves corrosion resistance and surface hardness.
Quality Control
Every batch of titanium screws is rigorously tested for quality assurance. This includes checks for tensile strength, corrosion resistance, and dimensional accuracy.
Choosing the Right Titanium Screw Manufacturer
Selecting the right titanium screw manufacturers is crucial for ensuring high-quality products that meet specific requirements. Here are some factors to consider:
Experience and Reputation
Choose manufacturers with a proven track record and positive reviews. They are likely to adhere to industry standards and deliver reliable products.
Production Capabilities
Ensure the manufacturer has advanced machinery and technology capable of scaling production according to your needs.
Customization Options
Look for manufacturers that offer customization, allowing you to specify sizes, grades, and other specifications for your screws.
Certifications
Industry certifications, such as ISO 9001, signify quality management standards, further ensuring product reliability.
Environmental Impact Consideration
The production of titanium screws, while beneficial for numerous applications, also raises questions regarding environmental impact. Sustainable manufacturing practices are essential:
- Recycling: Titanium is highly recyclable, which can reduce resource consumption.
- Energy Efficiency: Adopting energy-efficient manufacturing techniques helps lower carbon footprints.
- Waste Management: Proper handling of waste generated during production can minimize environmental impact.
Future Trends in Titanium Screws
As technology advances, so too will the manufacturing and application of titanium screws. Here are some upcoming trends to watch:
Additive Manufacturing
Also known as 3D printing, additive manufacturing is set to revolutionize how titanium screws are produced, allowing for more complex designs and reduced waste.
Increased Use of Advanced Materials
Research into composites and other advanced materials may lead to even lighter and stronger alternatives in the fastener market.
Global Sustainability Initiatives
With an increasing focus on sustainability, there will likely be a push towards greener manufacturing practices in the titanium industry.
Conclusion
In conclusion, the realm of titanium screw manufacturers is filled with potential and innovation. Understanding the advantages, applications, and manufacturing processes of titanium screws allows businesses and consumers to make informed decisions. As the demand for lightweight, strong, and corrosion-resistant fasteners continues to grow, titanium screws will undoubtedly play a pivotal role in various industries, from aerospace to medical applications.
For top-notch titanium fasteners, titaniumbolts.com is your go-to source, providing exceptional quality and a wide range of products tailored to your needs.