The Importance of Downhole Filters in Modern Industry
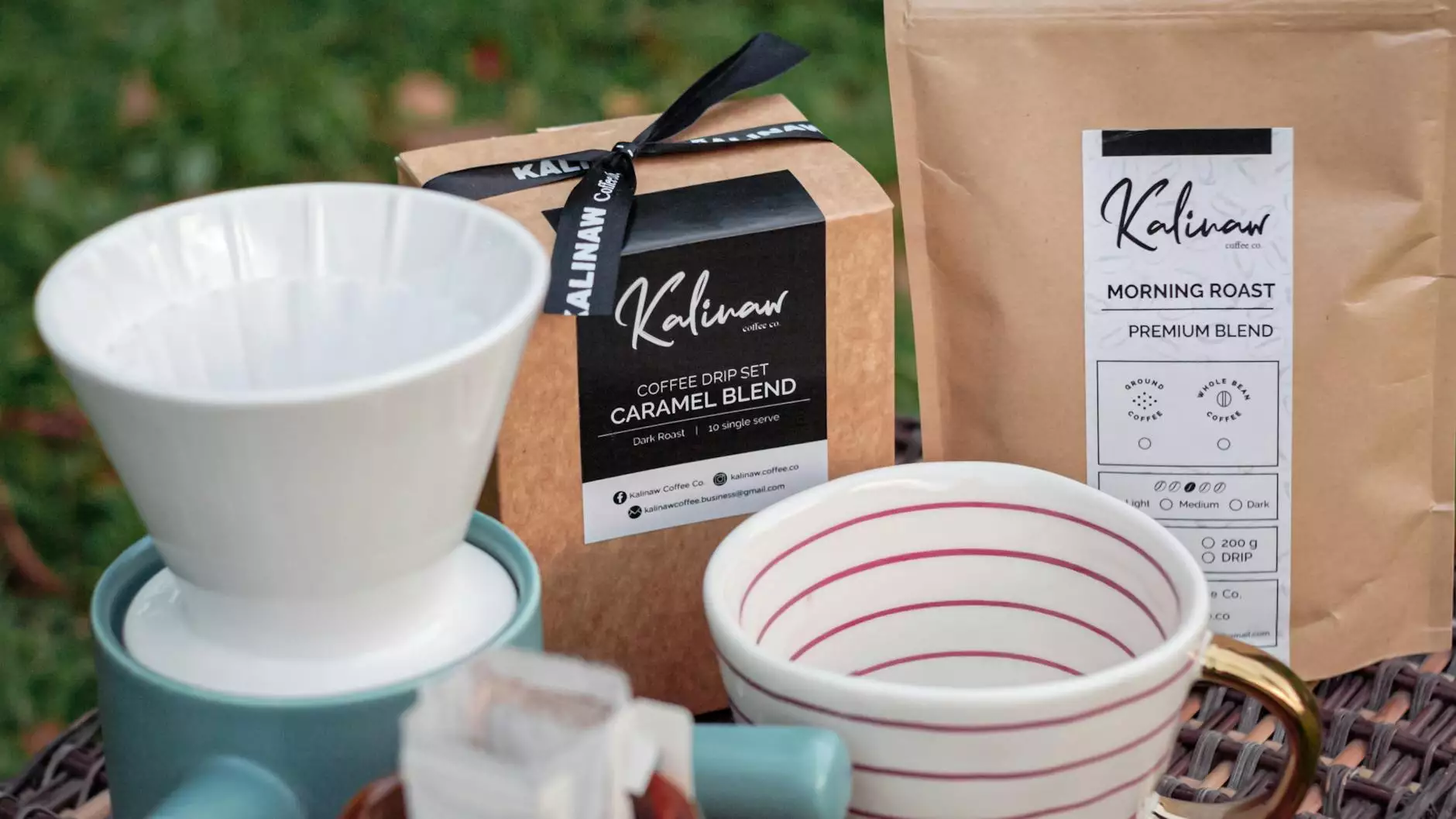
In today's fast-paced industrial environment, efficiency and performance are paramount. The use of advanced technologies and specialized equipment, such as downhole filters, plays a crucial role in the success of various sectors, notably in construction and drilling. This article will delve into the origins, functionalities, benefits, and future prospects of downhole filters, particularly within the context of Maverick Drilling's expertise in building supplies and machine & tool rental.
Understanding Downhole Filters
Downhole filters are incredible innovations used mainly in drilling operations to enhance the quality of fluid returning from the borehole to the surface. These filters work by effectively removing solid particulates and contamination, thereby ensuring that the drilling operations proceed smoothly and efficiently.
Key Functions of Downhole Filters
The fundamental purpose of downhole filters can be broken down into several key functions:
- Contaminant Removal: Filters trap and eliminate unwanted solids from drilling mud, thus protecting the conveyance systems and other equipment from damage.
- Fluid Quality Maintenance: Filters ensure that the drilling fluid maintains its desirable properties, such as viscosity and density, which are crucial for effective drilling.
- Operational Efficiency: By reducing wear and tear on pumps and other equipment, downhole filters contribute directly to lower operational costs.
The Benefits of Utilizing Downhole Filters
Implementing downhole filters in drilling operations yields numerous advantages, reinforcing their importance in the industry:
1. Enhanced Performance
Downhole filters contribute significantly to improved drilling performance. By ensuring that the drilling fluid remains free of debris and contamination, operators can maintain optimal drilling parameters, which leads to faster and more effective drilling cycles.
2. Cost-Effectiveness
Though there may be an initial investment in these filters, the reduction in repairs and replacements of equipment due to less wear and tear results in substantial long-term savings. Additionally, the efficient use of drilling fluids decreases operational costs.
3. Increased Equipment Lifespan
By filtering out harmful solids from the drilling fluid, downhole filters help extend the lifetime of pumps, motors, and other critical drilling components. This contributes to a more sustainable operation, minimizing the environmental impact associated with equipment disposal.
4. Safety Enhancements
By maintaining the integrity of the drilling fluid, downhole filters also contribute to safety improvements in drilling operations. Clean fluids reduce the risk of blowouts and other hazardous incidents.
Choosing the Right Downhole Filter
Selecting the appropriate downhole filter for a specific application is crucial. Here are some essential factors to consider:
- Filter Size: Ensure that the filter size matches the specifications required for your drilling operation.
- Filtration Rating: Choose a filtration rating that will effectively remove the desired solid particles while maintaining fluid flow compliance.
- Material Composition: Consider the materials used for the filters, especially their durability and resistance to corrosion and thermal conditions.
- Maintenance Requirements: Look for filters that offer easy maintenance to reduce downtime during drilling operations.
Innovations in Downhole Filter Technology
As industries advance, so does the technology behind downhole filters. Recent innovations include:
1. Advanced Materials
New materials offer superior filtration capabilities and resistant properties. For instance, the use of composite materials has led to filters that are both lightweight and extremely durable, which conserves energy in drilling operations.
2. Smart Filters
Technology is moving towards smart filters that can provide real-time data on the filtration process, alerting operators about potential clogs or maintenance needs before they become major issues.
Case Studies: Downhole Filters in Action
To illustrate the impact of downhole filters, we can examine a few case studies where their implementation drastically changed the drilling environment.
1. Offshore Drilling Operations
In a significant offshore drilling project, the integration of advanced downhole filters allowed for the efficient removal of scale and debris from seawater used in drilling mud. This not only enhanced the consistency of the drilling fluid but also increased the speed of drilling operations by 30%.
2. Land-based Operations
In a rugged land-based drilling setting, the use of downhole filters enabled operators to effectively manage challenging terrain conditions without frequent interruptions. By maintaining fluid quality, these filters saved hundreds of hours in downtime and significantly reduced operational expenses.
Environmental Impact of Downhole Filters
Today, companies are increasingly aware of their environmental responsibility. Downhole filters play a pivotal role in minimizing the ecological footprint of drilling operations.
1. Reduced Waste
By ensuring that drilling fluids are properly filtered, companies can minimize waste disposal needs, thereby lessening the strain on landfill sites and lowering the carbon footprint associated with waste management.
2. Water Conservation
Effective filtration allows for the recycling of drilling fluids, thereby conserving water, an essential resource. This is particularly vital in regions where water scarcity is an issue.
Conclusion
In conclusion, downhole filters are an invaluable component of the drilling industry, capable of enhancing operational efficiency, increasing safety, and promoting sustainable practices. As Maverick Drilling continues to evolve and lead in the fields of building supplies and machine & tool rental, embracing innovative technologies such as downhole filters will be crucial in ensuring success and competitiveness in an ever-changing market.
For businesses looking to optimize their operations, investing in high-quality downhole filters is not just a choice—it’s a necessity. With ongoing advancements in technology, the future of downhole filters looks promising, presenting exciting opportunities for various industries.